For inspections of photovoltaic systems, the use of drones is a decisive factor in reducing the time required. Our partner UCAIR uses drones in combination with our project management software HORIZON to map the entire inspection workflow. UCAIR’s numerous inspection missions enabled them to evaluate the data obtained in a statistic report and thus to develop a study on the frequency of defects in PV systems.
UAVs quicken inspections of photovoltaic systems
As a result, 128 inspections in 2017 revealed defects in 75% of existing PV systems. The most frequently found defects were hotspots, which are very easy to locate using a thermal imaging camera. UCAIR prefers to use drones for this type of inspection because they work much faster than technicians with handheld cameras. PV systems up to 10 MWp (Megawatt peak) can be inspected in a single day using an inspection drone.
The five most common defects in PV systems
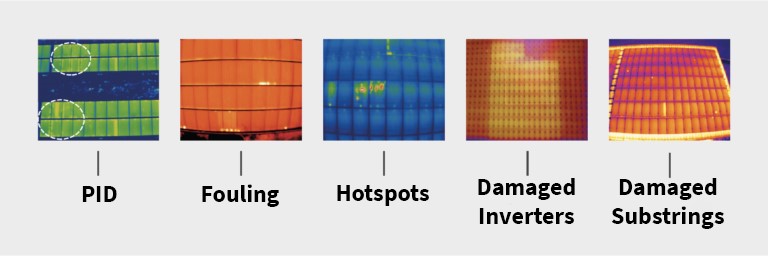
5 images of most common issues with pv systems (Source: UCAIR)
PID
The so-called potential difference between solar cells and grounding. The results are excessively high negative voltages between the cells and the frame of the individual modules. In the worst case, this can lead to local short circuits, which can trigger a fire.
Hotspots
The causes for hotspots are contamination, mechanical damage and module-internal faults, such as unclean solder joints. These lead to a reduction of the resistance in a cell. This increases the voltage and can lead to a short circuit. Hotspots should, therefore, be repaired immediately as there is an imminent risk of fire.
Contamination
Dirty modules generate little or no power. This can be caused by dust, dead insects or bird droppings. The modules are normally inclined so that most of the dirt is usually cleaned naturally when it rains. Nevertheless, in dry summers, the dirt may settle on the system and cleaning may be necessary. In addition, the panels on some photovoltaic systems have an angle of inclination that is too small. As a result, more dirt remains on them and is not washed away in the rain.
Damaged Substrings
Solar modules usually consist of 3 substrings. If one of these strings fails, this is clearly visible on a thermograph (see figure above). Defects in these substrates are often caused by defective bypass diodes. Since each module is normally divided into 3 parts, the performance of this module is reduced by 33 % if one of the substrings is defective.
The larger the system, the greater the probability of a defect
According to the UCAIR study, the probability of defects or soiling is 100% for systems with an output of more than 100 kWp.
Defects and soiling are clearly visible on thermal images (so-called thermographs).
Since thermographic cameras detect pixel-precise temperature differences, a damaged area can be clearly identified before maintenance or after an inspection and the fault or contamination can thus be solved. The efficiency of the system is thus increased again, and the resulting yield is maximized.
Cleaning PV systems
Contaminated photovoltaic systems yield less because the individual cells cannot reach their full efficiency. In order to determine whether a system is operating efficiently, its yield must first be checked. However, pollution is a gradual process and the operator often forgets the plant’s reference value. Here, a thermographic inspection can provide clarity and visualize contamination. Especially the inspection of large plants can be very time-consuming. Even more, if they are inspected by a technician equipped with a handheld camera. Drones can improve this workflow because they can fly above large areas in a very short time. The data recorded by the drone’s thermal imaging camera is also more detailed. The reason for this is the much more advantageous angle a drone can take compared to a technician with a handheld camera. For example, it is much easier to avoid reflections in the shots.
The environment of a PV system also plays a major role in pollution. If there are many trees in the vicinity, pollen, leaves, and needles can pollute the system. Since birds often nest on trees, the probability that a photovoltaic system is polluted by feces also increases.
In drier areas, more frequent cleaning is necessary as rain is too rare to clean the system naturally.
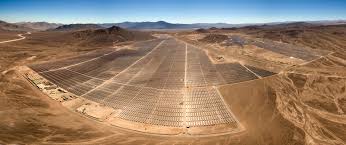
146 MWp PV-plant in the Atacama desert, shot by Antonio Garcia
UCAIR, therefore, recommends that PV systems should be inspected either when the yield is lost or at least every 1-2 years. However, the maintenance of the system should always be accompanied by a prior inspection in order to detect not only the contamination but also all defects. The cleaning of a system costs approx. 1.50 – 2.50 € per square meter. These costs can be amortized however because in a period of two to three years a PV plant can reach a loss of up to 15% – alone by contamination.
If one adds to this the 75% faulty systems that were detected during UCAIR´s inspections, one can only conclude that a regular inspection for solar and photovoltaic systems is indispensable.
Integrated project management to further improve the workflow
Drones facilitate inspections of photovoltaic systems, but a drone is only a tool that has to be integrated into the daily work routine. Here our software HORIZON offers the basis. The procedure is very simple: The drone missions can be planned completely within HORIZON with just a few clicks. UCAIR uses the possibility of our data sources to determine whether a permit to fly is required for the individual flight. With our validation, it is also possible to simplify the approval process with the legislator. By integrating more than 165 valid sources for geodata, our database is currently the most comprehensive on the market. This makes it possible to plan very precisely and avoid possible no-fly zones.
Another advantage of our solution is fleet management. For a company like UCAIR, which has numerous drones and pilots, this integrated management is a clear advantage over other methods of inventory cataloging. The pilots, in turn, can directly view their flight route and call up the entire project data.
After the flight, the results can be loaded directly back into the software and evaluated by an expert from any location. This makes it possible to spatially separate the activities of the pilot and inspector so that pilots can be deployed throughout Germany, while the data evaluation takes place at the company headquarters. In addition, the measurement results can be transmitted to the customer via HORIZON as well.
The use case of HORIZON at our partner UCAIR shows how our project management software can be integrated into daily operations and thus supports the coordination of drone missions from planning to flying and analysis of the collected data.
The FlyNex Team